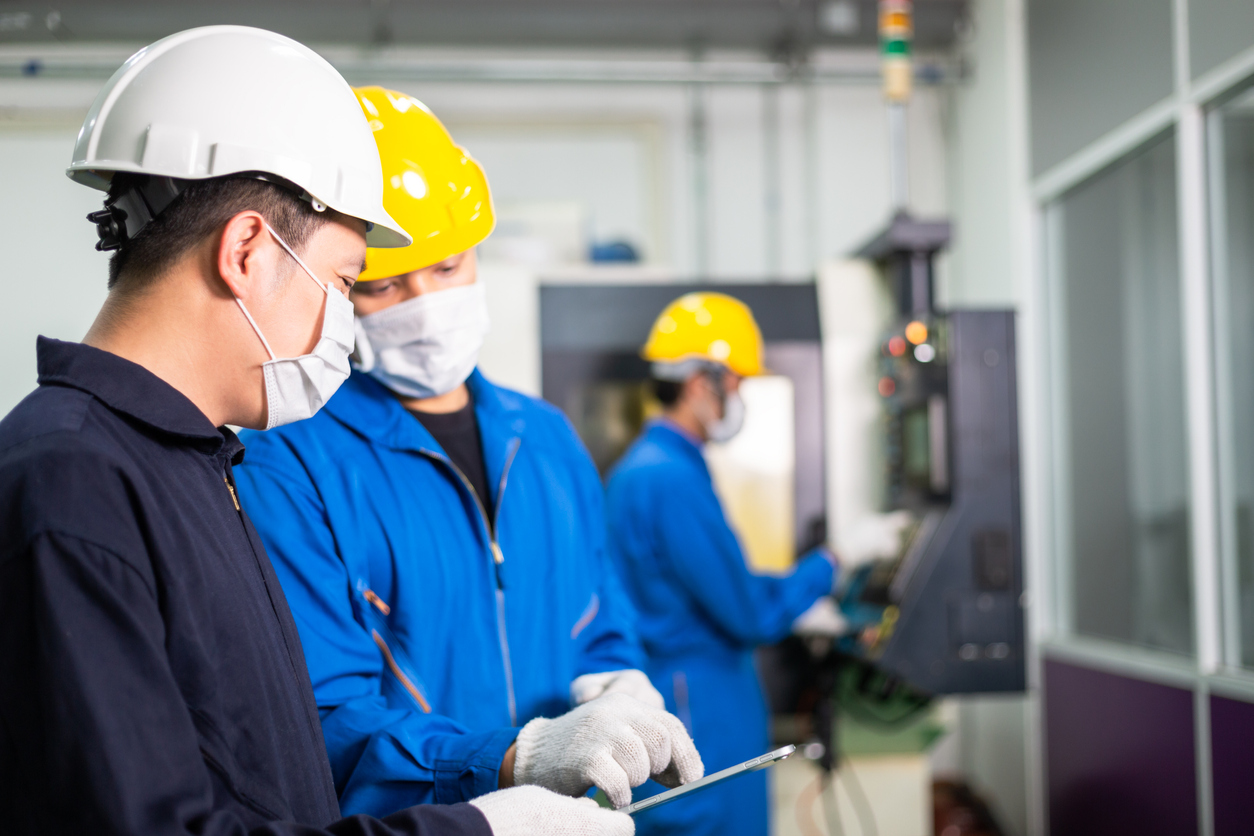
Nearly everything worth keeping requires maintenance—from our dental health to our cars, our homes to our pets. When we take care of the things we cherish or need each day, those things remain available for us. So while upkeep can be frustrating at times, that effort nearly always pays off.
It’s not too much of a stretch to say that being responsible for something really means maintaining (or taking care of) it. So, when your business, your productivity, and your safety depend on heavy machinery, maintaining that machinery is a wise business decision—both for the present and the future.
Industrial maintenance services come in nearly too many forms to list. So, what kind of maintenance is best for your machinery and business? Let’s take a look.
Preventive Maintenance VS Predictive Maintenance in Dallas & Fort Worth, TX
At Cornerstone Mechanical, Inc., we’ve been honing our corrective, predictive, and preventive maintenance services since 1995. In those three decades, we’ve developed maintenance plans to address the needs of every heavy machine throughout Dallas and Fort Worth, TX.
Learn more about the right kind of maintenance for you and give us a call today at (214) 570-9498 to schedule service.
What is Preventive Maintenance?
Preventive maintenance is a form of regular maintenance that involves replacement parts, comprehensive inspections, and tune-ups to prevent disruptions or major malfunctions before they occur.
Without regular inspections, your machines are at greater risk of failure. This simple assumption guides preventive maintenance programs for machinery of all kinds—from centrifugal pumps to cooling towers.
By scheduling preventive maintenance around your needs, you’re avoiding emergency repairs at an hour beyond your knowing or choosing. That alone saves you both time and money. But preventive maintenance has other advantages, too.
The top benefits of preventive maintenance include:
- Increases lifespan of heavy equipment
- Makes productivity and output more reliable/predictable
- Prevents work stoppages and expensive, emergency repairs
- Maximizes safety for employees and premises
- More
What is Predictive Maintenance?
Predictive maintenance relies on testing to determine the ideal time for equipment maintenance. By inspecting currently operational machinery, predictive maintenance technicians are able to pinpoint the best moment for replacement parts, tune-ups, further inspections, and even major work.
Predictive maintenance testing uses key performance indicators and real-time metrics to analyze the need for maintenance or risk of failure. Those tests may include:
- Routine vibration monitoring
- Infrared thermography
- Condition monitoring (also called continuous asset monitoring)
- Laser alignment
- DragonVision™ Video Deflection Technology
- More
Some business owners/machine operators prefer predictive maintenance to paying for several routine maintenance visits over the months or years. When used wisely, predictive maintenance can save you time and money, though this depends on the type and age of your machinery as well as the demands you place on it.
What’s the Difference Between Preventive & Predictive Maintenance?
While preventive maintenance assumes a baseline of wear and tear, predictive maintenance uses diagnostic testing to predict when wear and tear will reach a critical point. Both services are vital to maintaining heavy machinery, and each has its own benefits and advantages.
If your machinery is fickle, sensitive, or prone to minor disruptions that lead to eventual failures, preventive maintenance may be best. On the other hand, for machinery that’s more reliable on average, predictive maintenance may be all you need. The ideal form of industrial maintenance for you and your operation comes down to your equipment and tolerance for risk.
When something does break, we use yet another form of maintenance—corrective maintenance.
What is Corrective Maintenance?
Corrective maintenance is the most recognizable form of heavy machinery upkeep. True to its name, corrective maintenance doesn’t prevent or predict so much as it repairs.
When an individual component, several components, or whole systems fail, corrective maintenance technicians are brought in to replace the damaged parts, restart the machinery, and ensure that everything works properly.
Schedule The Right Kind of Maintenance For You
Unsure which form of maintenance would be most beneficial for you? No worries! At Cornerstone Mechanical, we can evaluate your equipment and your needs to arrive at the perfect maintenance schedule.
For the last three decades and counting, Cornerstone technicians have kept the wheels, rotors, fans, and centrifugal pumps of industry turning throughout Dallas and Fort Worth. When so much depends on the fitness and dependability of your machinery, so much depends on your schedule of maintenance, too.
Speak with an expert about your operation and maintenance needs today by calling us at (214) 570-9498 or contacting us online!
Maintained Machinery Supports Predictable Profits & Output in Dallas & Fort Worth, TX
Acknowledging the need for maintenance is the first step in setting your machinery and your operation up for success. Just like brushing our teeth or getting the oil changed in our cars, industrial maintenance can often feel like a headache. But with the right maintenance partners on your side, you can take routine inspections off your plate and put them onto ours instead. Let a Cornerstone technician suggest the best course of action for your operation today!