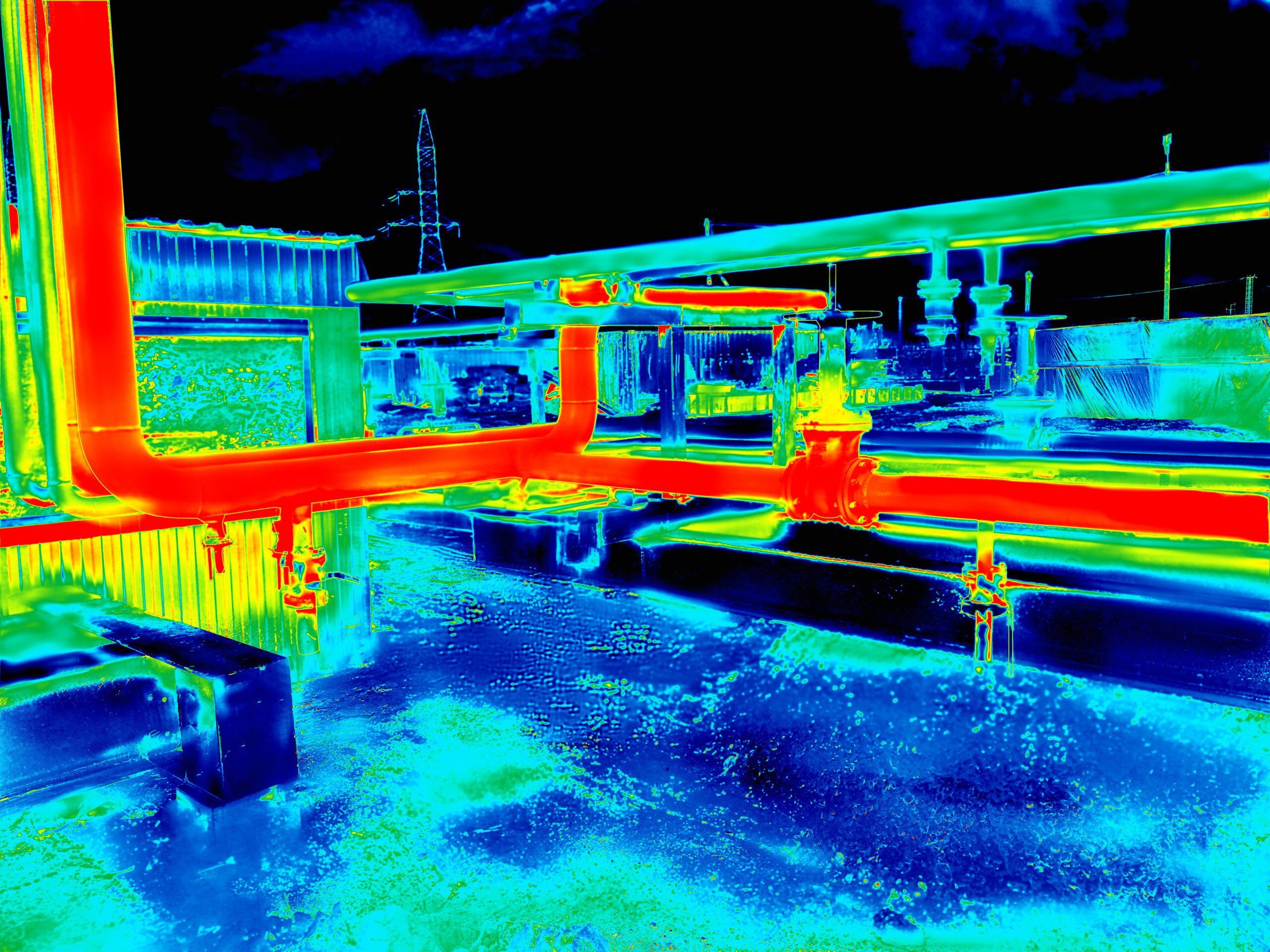
Predictive maintenance has revolutionized the manufacturing industry by allowing businesses to anticipate and address potential equipment failures before they occur. This proactive approach reduces downtime, enhances safety, and improves overall operational efficiency. At the core of predictive maintenance is a suite of advanced tools, with infrared thermography emerging as one of the most valuable.
Infrared thermography uses thermal imaging to detect heat patterns in machinery, identifying anomalies that could signal potential issues. In this blog, we’ll explore how infrared thermography works, its applications in condition monitoring, and the benefits it brings to predictive maintenance in the manufacturing industry. For rotating equipment such as motors, bearings, and pumps, this non-invasive technology plays a critical role in ensuring optimal performance and reliability.
A Closer Look at Infrared Thermography
Infrared thermography is a diagnostic technique that uses thermal cameras to detect and visualize heat emitted by equipment. All objects emit infrared radiation as heat, which is invisible to the naked eye but can be captured and translated into detailed thermal images. These images reveal temperature variations that may indicate normal operation or potential issues.
In rotating equipment, heat anomalies often signal underlying problems such as misaligned components, excessive friction, or electrical faults. For example, overheating in bearings could point to inadequate lubrication, while uneven heat distribution in motors might indicate an internal failure. By analyzing these heat patterns, maintenance teams can pinpoint problems before they escalate into costly breakdowns.
One of the key advantages of infrared thermography is its non-invasive nature. Inspections can be performed while machinery is in operation, eliminating the need for downtime. This allows maintenance teams to monitor equipment in real time and prioritize repairs based on the severity of detected issues, improving overall operational efficiency and safety.
Infrared Thermography Applied to Predictive Maintenance
Infrared thermography has become a cornerstone of condition monitoring in predictive maintenance, particularly for rotating equipment. By capturing and analyzing thermal images, maintenance teams can assess the health of critical components and address issues before they lead to equipment failure.
Common Applications
- Monitoring Bearings: Bearings are essential for the smooth operation of rotating equipment, but they are also prone to wear and overheating. Thermography detects abnormal heat patterns caused by misalignment, overloading, or insufficient lubrication, enabling teams to perform targeted maintenance.
- Monitoring Gearboxes: Gearboxes are critical components in many industrial systems, but they are prone to issues like excessive friction, misalignment, or inadequate lubrication. Infrared thermography identifies heat irregularities that signal early signs of wear and tear.
- Inspecting Motors and Pumps: Uneven heat distribution in motors and pumps often indicates issues like electrical imbalances, internal defects, or mechanical strain. Infrared imaging provides early warnings, allowing for timely repairs or replacements.
- Assessing Hydraulics Systems: Hydraulics play a key role in industrial machinery, but overheating in pumps, valves, or other components can indicate inefficiencies or hidden leaks. Infrared thermography allows for non-invasive monitoring of heat distribution within hydraulic systems, ensuring they function efficiently and avoiding costly repairs.
- Electrical System Analysis: Infrared thermography identifies hotspots in electrical components such as circuit breakers, connectors, and panels. These hotspots may signal loose connections, overloaded circuits, or failing components, helping prevent fires and equipment malfunctions.
- Ensuring HVAC Efficiency: In manufacturing environments, infrared thermography can also monitor HVAC systems, determining whether heating and cooling units are operating efficiently and supporting the health of the facility’s operations.
- Inspecting Conveyor Belts: Conveyor belts are essential for transporting materials, but issues like misaligned rollers or excessive tension can lead to overheating and system inefficiencies. Infrared thermography detects abnormal heat patterns along the belt and its components, helping to pinpoint problem areas.
Benefits of Infrared Thermography for Rotating Equipment Maintenance
Enhanced Safety
Infrared thermography improves workplace safety by detecting potential equipment failures before they become dangerous. For instance, identifying overheating bearings, electrical hotspots, or misaligned components reduces the risk of fires, machinery breakdowns, and accidents that could harm workers or disrupt operations. By addressing these issues proactively, businesses create a safer environment for employees while avoiding unexpected emergencies.
Energy Efficiency
Abnormal heat patterns often indicate inefficiencies in energy use, such as overworked motors or improperly functioning components. Addressing these inefficiencies through timely maintenance keeps machinery operating at peak efficiency, reducing energy consumption and operational costs. Enhanced energy efficiency also minimizes the environmental impact of industrial processes, helping businesses meet sustainability goals and comply with regulatory standards.
Minimal Disruption to Operations
One of the greatest advantages of infrared thermography is its ability to conduct inspections while equipment is running. This non-invasive approach minimizes production delays, allowing maintenance teams to gather essential data without interrupting operations. Businesses can maintain productivity and optimize maintenance schedules simultaneously, making inspections an integral part of seamless operations.
Data-Driven Decision Making
Thermal imaging provides precise, actionable insights into equipment performance, allowing maintenance teams to prioritize repairs based on urgency and potential impact. With detailed data, businesses can allocate resources effectively, plan maintenance schedules efficiently, and give attention to critical equipment before minor issues escalate into costly problems. This data-backed approach fosters smarter, more strategic maintenance decisions.
Extended Equipment Lifespan
Regular monitoring with infrared thermography allows for the early detection of wear and tear, so teams can resolve minor issues before they develop into major failures. This proactive approach reduces stress on equipment components, optimizing their performance and longevity. Over time, this results in fewer replacements, lower maintenance costs, and increased return on investment for industrial equipment.
Trust Cornerstone Mechanical for Predictive Maintenance Solutions
At Cornerstone Mechanical, we specialize in providing advanced condition monitoring and predictive maintenance services tailored to the unique needs of our clients. Whether you’re maintaining rotating equipment like motors and bearings or critical electrical systems, our expert team leverages the latest technologies to help businesses identify and address potential issues before they escalate.
Our approach minimizes downtime, reduces maintenance costs, and extends the lifespan of your equipment. With a focus on accuracy and efficiency, we’re dedicated to helping you maintain smooth operations and maximize your facility’s productivity.
Your Infrared Thermography Experts in Texas
Cornerstone Mechanical is proud to offer comprehensive predictive maintenance services, including infrared thermography, to businesses across Texas. With our expertise in condition monitoring and advanced maintenance tools, we help keep your equipment running reliably and efficiently. Call us at 214-570-9498 or reach out online today to learn how we can support your maintenance goals and provide the solutions you need for a safer, more efficient operation.