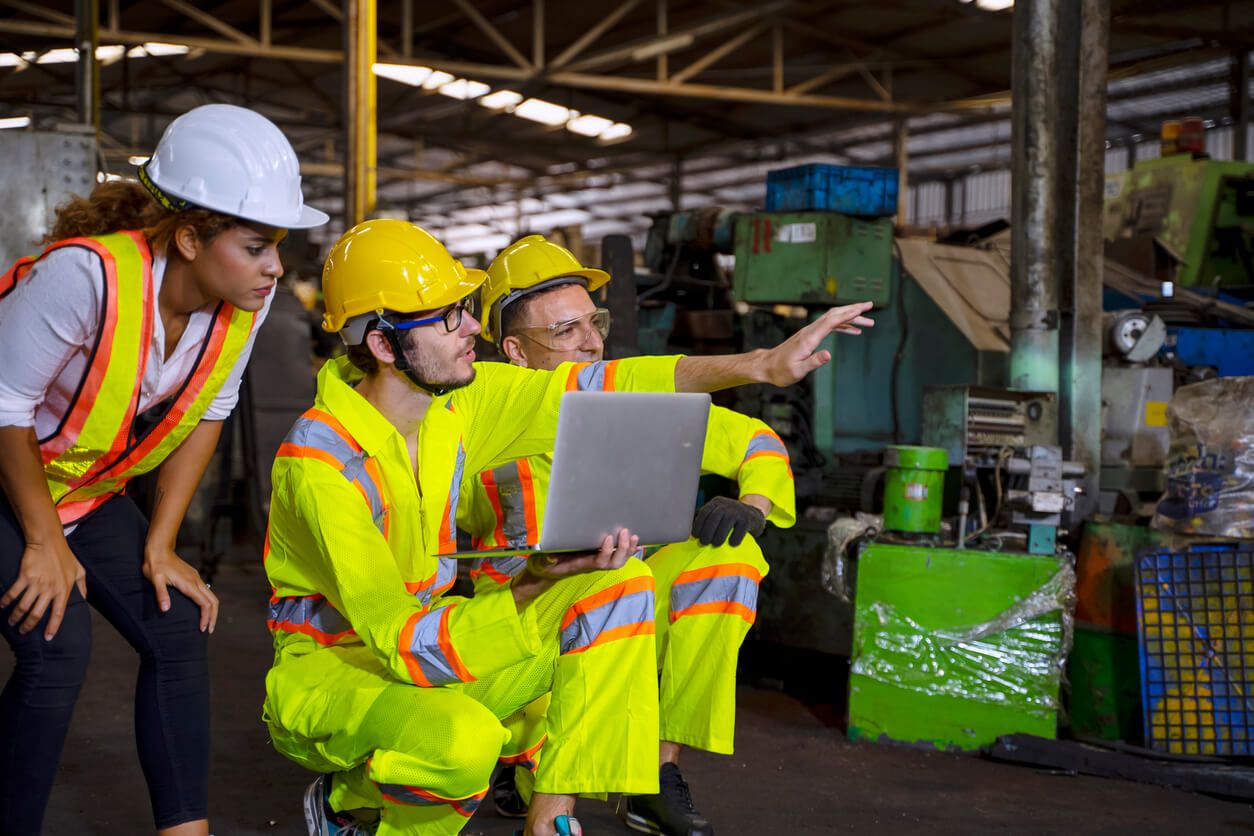
Unscheduled maintenance can be a financial nightmare for businesses, leading to a cascade of costs and disruptions. The immediate expense of emergency repairs is just the tip of the iceberg, as unexpected breakdowns also result in lost operating hours and productivity, not to mention the additional costs of paying employees during downtime.
With preventive maintenance, businesses can avoid the hefty price tag and operational setbacks associated with reactive repairs. In this post, we’ll dig into the substantial costs of unscheduled maintenance and highlight how adopting a preventive approach is a matter of operational efficiency and financial prudence.
The High Price of Unexpected Breakdowns
The financial repercussions of unexpected breakdowns in a business setting are extensive and multifaceted. Initially, there’s the direct cost of lost operating hours where machinery or equipment stands idle, halting production or services and leading to immediate revenue loss. Beyond the immediate loss of productivity, businesses face the additional burden of paying employees who are unable to work effectively due to equipment failure.
Then comes the emergency repair bill, often exorbitant due to the urgency and necessity of immediate service to resume operations. These repairs, typically more costly than scheduled maintenance, can significantly impact a company’s budget. Additionally, the knock-on effect on productivity and quarterly goals might necessitate overtime pay, extended operating hours, and other compensatory measures, further inflating expenses.
The cumulative cost of unscheduled maintenance extends far beyond the initial repair bill, impacting the overall financial health and operational stability of a business, making a strong case for the importance of preventive maintenance strategies.
Preventive vs. Predictive vs. Corrective Maintenance
Understanding the distinctions between preventive, predictive, and corrective maintenance is crucial for effective asset management and cost control in any business. Here’s a quick rundown.
Preventive maintenance involves regular, scheduled checks and servicing of equipment to prevent unexpected failures. This proactive approach is designed to keep machinery running efficiently and avoid the disruptions of unplanned downtime. By regularly replacing parts before they fail and performing routine upkeep, businesses can reduce the likelihood of emergency breakdowns and extend the lifespan of their equipment.
Predictive maintenance takes a more data-driven approach, using technology to monitor equipment performance in real time and predict when maintenance should be performed. Sensors and analytics can detect potential issues before they become serious problems, allowing for maintenance to be conducted just in time to prevent failure. Predictive maintenance optimizes the maintenance schedule based on actual equipment conditions, potentially saving more on maintenance costs than traditional preventive strategies.
Corrective maintenance, on the other hand, is a reactive approach, where repairs and maintenance are performed only after equipment has failed. While sometimes necessary, this approach often leads to higher costs and more significant operational disruptions compared to preventive and predictive maintenance. Corrective maintenance can be seen as a last-resort measure rather than a strategic approach to equipment management.
Economic Benefits of Preventive Maintenance
Firstly, preventive maintenance extends the lifespan of machinery and equipment, ensuring they operate efficiently for longer periods. This reliability reduces the need for frequent replacements and capital investments, providing a direct cost benefit. Regular upkeep helps identify potential issues early, allowing for minor repairs before they escalate into major problems that require expensive and extensive corrective actions.
Also, preventive maintenance leads to more predictable budgeting for maintenance costs. Companies can plan and allocate resources more effectively, avoiding the financial shock of unexpected repair bills. This predictability also contributes to smoother operational processes, as equipment is less likely to fail unexpectedly, ensuring consistent productivity and revenue generation.
Another significant advantage is optimizing equipment performance. Well-maintained machines operate more efficiently, consume less energy, and have lower operating costs. This increased efficiency reduces utility costs and contributes to environmental sustainability.
Overall, preventive maintenance is a cost-effective strategy that not only saves money on immediate repairs but also contributes to the overall financial health of a business by improving equipment longevity, enhancing operational efficiency, and ensuring predictable maintenance expenses.
Strategies for Avoiding Unscheduled Downtime
- Regular Inspections and Servicing: Schedule regular checks and servicing of all critical equipment to identify and address potential issues before they lead to breakdowns.
- Invest in Predictive Maintenance Tools: Utilize technology like sensors and monitoring systems to predict equipment failures before they occur, allowing for timely and less costly interventions.
- Train Staff on Equipment Use and Maintenance: Ensure that all employees are trained in the proper use and basic maintenance of machinery, which can prevent misuse and early wear and tear.
- Establish a Maintenance Schedule: Create and adhere to a comprehensive maintenance schedule based on the manufacturer’s recommendations and historical performance data of the equipment.
- Keep Spare Parts Inventory: Keep a stock of essential spare parts for critical equipment to avoid delays in repairs and reduce downtime during unscheduled maintenance.
Investing in Maintenance for Long-Term Savings
Investing in regular maintenance is a strategic decision that pays dividends in the long run. Proactive maintenance practices like preventive and predictive maintenance reduce the immediate costs associated with emergency repairs and contribute to sustained operational efficiency and financial savings over time.
Leading Preventive Maintenance Services in Texas
In the Lone Star State, Cornerstone Mechanical leads the way in providing top-tier preventive maintenance services. Partnering with Cornerstone ensures that your equipment is in optimal condition, minimizing downtime and extending the lifespan of your assets and the value your organization gets from them. Think about the benefits that preventative maintenance can bring your business’s operational future, then either reach out online or call us at 214-570-9498 to get started.